1. Scope
Till now I have confined myself to the design and construction of small Stirling models only to be able to exhibit their tricks in a living room setting. I consider them more or less as technical trinkets, so the focus is more on the design and safe operation, other than on high power and exceptional performance.
So my experiences with Stirling engines are limited to this kind of little models.
Below a sketch of a Stirling principle; click here for more details about the Stirling principle.
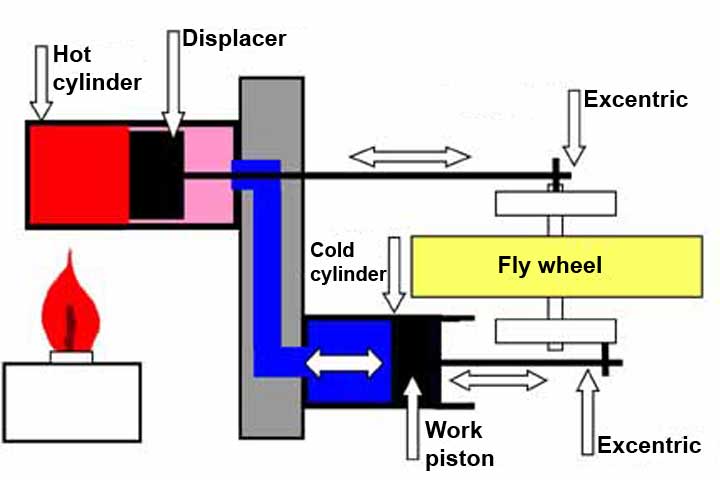
2. The "value" of a Stirling model
Compared to steam and Internal Combustion (IC) engines Stirling engines have a relatively low power because the pressure on the working piston is only a fraction of an absolute atmosphere. For small models one even must take take special measures to let them run smoothly and reliable without any external load. Don't expect to drive anything significant with it, unless there major decelerations are applied.
But this objection disappears completely when one have an eye for the other fascinations of Stirling model engines. They often impress with their surprising simplicity. Furthermore, they are very "friendly", not needing heavy fires, high pressures, steam , condensate spalling tendencies and so forth. It is easily possible to let them run them on a small candle flame and even on a cup with hot water, coffee or tea. It is sometimes even possible to let them run on a warm human hand.
So very friendly and straightforward harnesses that call for wonder and admiration at a demonstration, even for non-technical orientated spectators. It is probably no coincidence that I get a lot of requests from colleague model builders for drawing plans to make these models and to impress their family and friends with it. Serial production is usually not the style of a modeller, but sometimes such a Stirling model is a unique and appreciated gift for a good friend. On average the hours to spend for making these kind of Stirling models is anywhere between 50 to 70 net man hours.
3. Tips when creating a Stirling model
1. Because of the low power it is important that frictions and other counter-acting forces are limited to a minimum. Especially for the fast rotating parts is advisable to apply little ball bearings from what oil and grease are washed out with dry-cleaning naphtha. Also special attention should be paid to the parallelism and the alignment of all rotating parts and the parts relate to that. Never apply metal or rubber rings on the work piston because they introduce fatal friction !
2. The engine power is actually generated by the varying temperature of the enclosed air volume in the system and the associated pressure changes on the working piston. This air system should therefore be as leak free as possible. The challenge is to realize that along the displacer shaft and the working piston with a low as possible friction at the same time.
With regard to the displacer axis I have the best experience with standard rod material being smooth and with accurate diameter sliding in associated commercial bronze or steel bearing bushes. With home made graphite bushes I also have good experiences but it is sometimes difficult to get small amounts of graphite.
The bore in the work cylinder must be nicely cylindrical and smooth, which goes well with reaming as the last operation. The piston clearance must be so that it lingers with the thumb against the cylinder hole and then quickly falls down when the thumb is removed and that without oil lubrication! Lubricating of Stirling work pistons is disastrous in most cases, the engine will run bad with it and most of the time not at all. Oil reduces the wear and tear, but this does not arise in this type of small and slow running models.
3. The diameter of the displacer should be 1 to 2 mm smaller than the internal diameter of the hot cylinder, but this is not very critical. Along this gap between the displacer and its cylinder the air in the system cyclically is moving from the the hot to the cold zone of the system and vice versa, causing alternating pressures on the work piston with the result that is moves back and forth. In fact this delivers the power of the engine.
Of great importance is that displacer nowhere touches its the cylinder because it causes almost immediately fatal friction. The internal height or length of the hot cylinder should be just slightly larger than the stroke of the displacer, just enough to not touch anything. In principle a significantly larger space will cause some power loss but that seems not to be that critical.
4.The performance of a Stirling engine is mainly dependent on the temperature difference between the hot and cold cylinder. Depending on the construction it may be necessary to shield the cold cylinder from the flame that heats the hot cylinder to keep the temperature difference as large as possible.
5. With a relatively low volume content of the hot cylinder the temperature must be made several hundred degrees in order to realize enough air volume/pressure differences. In that case plastic cannot be applied as material for the hot cylinder of course. In my opinion and experience glass is the preferred material in that case, because the heat conduction through the glass to the cold part of the engine is very low. That also makes the construction easier because you don't need thermal isolating material between the hot cylinder and the cold cylinder. A glass cylinder in case of a high temperature Stirling can be easily fixed mechanically as well as air-tight at the same time with a rubber O-ring.
4. The ratio between the dimensions of displacer and work piston
The expansion and contraction of the air trapped in the engine is a rather complex thermodynamic process. Calculations are not very easy because the erasing air temperatures and hence the expansion and contraction of the air depends on a number of factors, such as the heat transfer coefficients of the used materials, the speed of the air with what it is moving from the hot to the cold zone and vice versa, and the flow pattern of the air in the system. This makes it difficult to calculate the precise and varying air temperatures and the pressure fluctuations. You can measure the temperatures of the hot and cold cylinders on the outside, but the temperature of the air inside will be considerable lower than that of the heated cylinder. But with a little "basic" physics and experiences you can surely get a good idea about the best relation between the dimensions of the displacer and the work piston:
1. The air volume of the system is not constant because the working piston in it goes up and down. This change in volume is thus totally determined by the choice of the diameter of the working piston and its stroke, and this is purely mechanically defined. Ideally, the change in volume of the air in the system by the heating and cooling thereof should be equal to the volume change of the working piston caused by the mechanical construction.
If the volume change by the warming-up and cooling of the air is greater than the volume change of the working piston (stroke x diameter) the engine will always run. However, because in this case the diameter of the working piston could have been somewhat greater the power of the engine is not entirely optimal.
If the volume increase as a result of the warming-up of the air is less than the volume change of the working piston (stroke x diameter) the piston will cause counter-acting forces at a certain point in the cycle because the piston will build up greater pressure, respectively lower under-pressure in the system than that which is the result of the warming-up and cooling of the air. In that case, the motor will run poorly or not at all.
As mentioned, an optimal situation is thus achieved when the changes in volume by the heating and the cooling of the air is equal to the volume changes of the working piston as a consequence of its diameter and stroke. However, this situation cannot be realized, at least not all the time because the temperature at which this occurs in fact is a "coincidence ".
To make sure that the engine is running always and reliable, this means that the diameter x stroke of the piston must be always made somewhat smaller than theoretically necessary, accepting some loss of power other than the risk of a bad or not running engine.
2. As said the theoretical calculation of the optimal geometry relations between the piston and the displacer is very difficult because of the rather complex thermodynamic process. In fact it is only possible to determine in practice if the selected ratios are well chosen as follows:
- Disconnect the driving rod of the working piston to the crankshaft so that this piston can move in its cylinder freely (with low friction course);
- Heat the warm cylinder and turn the flywheel around manually with the speed to be expected with the engine at normal operating temperature and then look at (or measure) the free stroke that the working piston is making in its cylinder due to the pressure changes in the system;
- The free stroke of the working piston must be at least equal to the stroke when the piston is coupled to the crankshaft , but should never be smaller. If the piston stroke it is smaller at this test the volume change of the working piston due to its diameter and/or stroke is too big.
3. The absolute volume expansion and contraction of the air that occurs due to the cyclic heating and cooling, is not only dependent on the temperature differences between the hot and cold cylinder, but also on the total air content in the system. The higher the temperature difference and/or the air content of the system the greater the change in volume/pressure will be. This therefore means that when the air volume is larger, the temperature difference can be lower to let the engine run. For example this is why Stirling models that can run on a human hand with very low temperatures always have a relatively large diameter (air volume) of the displacer cylinder. Conversely, it also means that when the volume in the displacer cylinder is made smaller the heating temperature must be higher, assuming that the temperature at the cold cylinder side is rather constant; just slightly higher than the ambient temperature under normal circumstances.
4. So it all has to do with the right ratio between the two volumes: the displacement volume of the working piston (diameter x stroke) that we will call here "Vp" and the total air volume of the system that we will call "Vs". So i t is not only the diameter of the piston and the displacer, although they determine these volumes of course significantly.
The total air volume in the system (Vs) is equal to the volume of the displacer cylinder (Vd) plus the stroke volume Vp of the working piston. The clearance of the displacer in its cylinder is small (somewhere in the order of 1 mm), so we can set the displacer cylinder volume for convenience equal to the diameter of the displacer and its stroke. We then get:
Vp = surface x stroke of the working piston piston;
Vd = surface x stroke of the displacer;
Vs = system volume = Vp + Vd
5. We introduce here the ratio term: R = Vs / Vp, or R = (Vd + Vp) / Vp. So this is the ratio between the total system volume and the displacement volume of the working piston. This term is well workable for the determination of the best ratio of the diameter and stroke of the displacer and working piston. The optimum value for R now only depends on the applied temperature difference between the hot displacer cylinder and cold working cylinder. The larger the applied temperature difference is the smaller the displacer volume can be with the same work cylinder due to the greater expansion of the air, and vice versa.
6. I here give the best values for the ratio term R in the case of the three common types of Stirling models, based on my experiences and assuming that the strokes of the displacer and the working piston are equal:
- For a " High Temperature Stirling " where a metal or glass hot cylinder is heated up to 300 to 400 degrees Celsius (or more) with a flame the optimum value for R is 1 to 2 , which means that diameter of the displacer can be about the same as the that of the working piston or slightly larger than that.
- For a " Stirling Coffee Cup ", which is warmed-up on a cup of boiling water to between 60 to 100 degrees Celsius maximum the optimum value for R is approximately 50, which means that the diameter of the displacer must be about 7x greater than the diameter of the working piston (square root of 50); again assuming that the strokes of the displacer and the working piston are equal as said before.
- For a " Low Temperature Stirling " that can run on a human hand for example with a temperature difference of about 10 degrees Celsius the value of R must be 100 at least, which means that the diameter of the displacer must be about 10 times larger than the diameter of the working piston.
Finally:
The value of R is therefore determined by four independent parameters of which most of the time two or even three are chosen in advance for practical reasons on basis of the desired dimensions of the motor and/or the available materials. It is my experience that for this type of Stirling models the stroke of the piston and displacer preferably should not be chosen too small because then the torque on the crankshaft becomes unfavourable causing a mechanical bad behaviour. A stroke between 10 and 20 mm for both the displacer and the working piston is a good choice in my opinion and a stroke of 5 mm is pretty much the minimum. There is usually little reason to make the strokes of the displacer and the working piston differently.
Thus with these assumptions (same strokes) there is only one choice to be made for the diameters of the piston and displacer. If one chooses one of the two diameters the other can be simply calculated with the relationship R = (Vd + Vp) / Vp where the value for R must be filled-in dependent on the type of Stirling (hot temperature, coffee cup or low temperature type).
5. The industrial significance of Stirling engines
Quite often I
get questions about practical applications of Stirling engines. My experience with Stirling engines is restricted to small models, and I'm not a scientist in this field, but I have a purely personal opinion anyhow about the prospects of the practical significance of Stirling engines:
Stirling engines have relatively very low power because the alternating pressure in the engine is very low: some tenth of an atmosphere, not more. This is about 20 times (ore more) lower than with steam engines or internal combustion engines where (dynamic) pressures like 10 to 20 bar are common.
The Stirling principle is already more than 100 years old and for more than a century numerous and very high classified scientists have tried to develop Stirling engines for useful practical applications. Till now there are hardly any convincing examples and if they exist they are marginal. The only way is to make them very big and/or to supply them with very much heat. I saw an industrial Stirling engine with more than 2 meters diameter driven by solar energy in a dessert pumping some 5 litres of water per hour; this to give you an idea. On YouTube you sometimes see these kind of experiments:
http://nl.youtube.com/watch?v=fUrB7KRvxUk
But this engine is driving hardly more than its own mechanism.
I also have seen an experimental project with many large Stirling engines in a desert operated by solar energy. But reportedly the investment was huge and the maintenance intensive and very expensive, at least compared to similar projects with solar panels that you can find more and more these days.
Medio 1900 there was a very big project at the famous Philips Physical Research Centre to investigate if it was possible to make a Stirling engine for practical use in what much time and money was invested. Apart from worldwide appreciated and valuable scientific articles it did not result in something practical except for a small laboratory instrument to produce very low temperatures on a small spot for special labatory investigations at these ultra low temperatures. Here the reverse process of a Stirling is applied: the engine is driven by an electro motor and the place where normally the heat is supplied becomes very cold. With an extreme good thermal isolation it is possible to make temperatures near the absolute zero point! But here the aim is not to make an efficient power supply but to make a small and practical laboratory equipment.
With very special techniques it is possible to generate a bit of power that otherwise would be lost. Currently there is development to use a Stirling engine in central heating systems using the temperature difference between the hot pipe and the cooler return line making some electricity to be added to the electrical supply for the circulation water pump. But despite much ingenuity, knowledge and special techniques the effects are not very spectacular for the time being; the most optimistic story is that the efficiency of the whole system will be improved with some 2%, while the extra costs and maintenance are so high that you hardly or not will have significant return of money.
The power of my small models will be less than 5 watts, just enough to drive their own mechanism, provided you make everything with very low friction. To give you an idea: my engines are absolutely unable to drive a bicycle dynamo.
Normal model Stirling engines only contain just air in the system. Filled with helium the yield is higher but the construction is disproportionately more difficult because everything has to be absolutely 100 % leak-proof for the very "thin" helium gas which require very special technique's, especially along the moving parts. For larger models one usually apply regenerators to boost the yield to 30% and in exceptional cases to 40 %; somewhat higher than steam or internal combustion engines. But this requires really special techniques that are absolutely not feasible for an amateur model builder I believe.
Stirling engines stimulate the imaginations already for ages because they can be fed with all kind of external heat sources like solar radiation, wood stoves, etc. But if one wants to use solar energy for practical applications solar cells or water boilers still are better alternatives because they don’t suffer from losses of mechanical frictions. That’s why solar cell panels are well known and rather common to make use of solar energy.
Another thing is that Stirling engines need a temperature difference between the hot side and the cold side of the engine. If you put such a Stirling on a stove or in an environment with hot solar radiation (like in a dessert) the cold side will warm up also gradually with the result that the engine will run slower and slower and finally stops most of the time.
So in my humble opinion it is hard (or even impossible) to make a reasonable small Stirling engine with real practical and significant power for the time being. If that should be the case there should be a lot of examples I think and I did not find any of them on the whole Internet till now, at least not for sale or drawing plan.
In short, I can recommend Stirling engines heartily as a model, but I will not encourage anyone to try making a real practical application for it because I really think it's doomed to a disappointment based on the existing theory and also because of the fact that an awful lot of work is done by the best scientists and industries without convincing success. If there should be Stirling engines with acceptable dimensions and cost price using solar energy or other waste heat that can produce a a reasonable amount of Watts (20 50, 100 or more) they would definitely be on sale somewhere, but that is absolutely not the case. You can look up on the entire Internet, but you can not find them, and that still makes you wonder. It is a common misunderstanding for the moment that you can make reasonable small Stirling engines for serious practical applications who can compete with several alternative solutions such as solar cell panels or wind mills.
But Stirling engines are beautiful things for modelling: easy to make, eye catching, very friendly, quite and safe to demonstrate on the table in your living room; success guaranteed while demonstrating them, even for not technical orientated spectators. But don’t expect much more from this (my) kind of Stirling models than driving their own mechanism and that only if you make them very accurate with the less possible frictions and almost leak free.
This is my experience and only my humble but sincere opinion. I will be glad to exchange that for another more positive one if that should be based on convincing evidence.