English
klik hier voor Nederlands
1. Scope
Till now date I have experiences with six flame-eaters and again with relatively small models. The construction of a flame-eater is even simpler than that of a Stirling engine, but the adjusting of it is appeared to me many times more difficult.
The principle of a flame-eater is extremely simple: hot flame gases which are sucked in the cylinder cool down at the moment the cylinder is closed by a slide valve which closes a flame hole in the cylinder head. This cooling creates a partial vacuum in the cylinder and the piston pressure it is pushed back through the outside air pressure and that delivers the (rather limited) power of the engine; that's why flame-eaters are called "Vacuum Engines" as well.
See the principle sketch below and go for more details to the concerning page on this website.
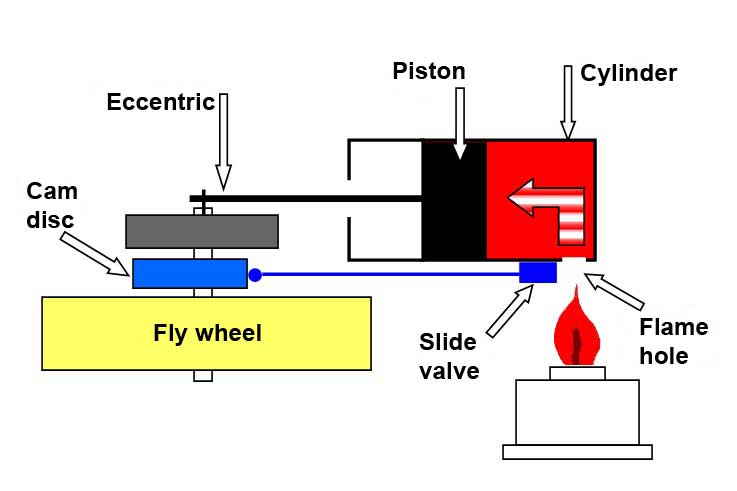
2. My experiences with Flame-eaters
More than Stirling engines flame-eaters have, compared to eg steam and internal combustion engines, relatively very low power because here the pressure on the working piston is only a fraction of an absolute atmosphere. Unlike a Stirling engine a flame-eater has only one power stroke, the other stroke is needed in order to suck-in new flame gases and during that stroke is no work done. This means that a flame-eater needs a somewhat heavier flywheel than a Stirling engine in order to help the engine over this dead stroke.
For small models, one should even take special measures to let the engine run unloaded smoothly and reliably. One should therefore not assume that a device of any format it can be driven with it unless the flame-eater is very large and there are major decelerations applied . Factual flame-eaters only are suitable as a nice model for modellers, I have never found any practical application for that. Not surprising, because apart from the fact that they have very little power they are also very sensitive for sucked-in false and cold outside air they pollute easiliy internally by the corrosive hot and wet sucked-in flame gases. This pollution usually occurs sooner or later too much friction of the piston in the cylinder so the engine must be cleaned regularly in order to keep the engine running.
But apart from the surprising simplicity the fascination of a flame-eater model is its tough (manlike) behaviour compared to Stirling models. Though they can be made as adornments they lend themselves less for demonstration in a living room area and as " freebies ". They require a fairly hefty alcohol flame and it is not advisable to demonstrate them on your walnut coffee table, especially if there is a risk that some spirits flows over the table which is not unthinkable! They also make much more noise which make them more attractive to more technically oriented audience sometimes.
Due to the rather simple construction making flame-eaters are perhaps easier (read: faster) to make than Stirling engines. But they are horrible nervous when it comes to the adjustment of it, at least with the usual external sliding valve which has to open and close the flame hole in the cylinder. It is my experience that one needs just as much time for well adjusting all the parameters than to build the motor itself. There are several critical parameters that must be adjusted one by one and at the same time to their optimum. The problem is that this adjustments can only be done successfully if the engine motor already tends to go running properly and that is only the case if all these parameters are reasonably close to their optimum; so a somewhat "chicken and egg" story. It may happen that you are changing something, while another parameter is not properly adjusted or created. Then you hit sometimes further afield and that makes you desperate sometimes. But it is also my experience that in situations like this persistence always wins, so one should not be discouraged by all this. With enough patience and systematical approach adjusting the engine is very well possible. Once all parameters are set to their optimum they run merrily and fairly reliable and will amaze especially modellers of steam engines that usually build more "manlike" models like steam engines. But apart from that any comparison holds on immediately.
The tips below mostly concern the adjustment and optimal tuning of flame-eaters with external valve; see section 4 for a flame-eater with internal valve.
3. Tips for construction and adjustments
1. Frictions.
Because of the low power it is important to limit frictions and other counteracting forces to a minimum. It is advisable to apply ball bearings on the flywheel shaft and on the connecting rod where it sits on the crank pin. These bearings often contain some grease making them somewhat heavy to rotate. This grease must be well washed out by turning turning them around in dry-cleaning naphtha. Grease is not necessary here because wear and tear is not to the order with these kind of small models.
Special attention should also must be paid to proper alignment of the connecting rods to prevent torsion and therefore unnecessary frictions on their pivot points.
The piston must be virtually airtight fit in its cylinder but also with the lowest possible friction. This can be verified as follows with a completely dry and clean piston and cylinder :
- With the cylinder in the vertical position and closed on top with your thumb the piston must stuck in the cylinder; then there is a sufficient air-tightness.
- When retrieving the thumb off the piston should spontaneously fall out of the cylinder; then the friction is low enough.
The sucked hot flame gases which also produce water vapour almost always cause some corrosion in the cylinder wall and/or on the piston. Quite soon some disposal arises than increasing the friction between the piston and the cylinder. As long as the engine runs it will not suffer from it, but if staying stationary for a longer time and being cooled it often happens that they will run bad or not at all after that. In that case the cylinder and the piston needs to be cleaned with e.g. some WD40 on a lint- free cloth. Incidentally, this is always advisable to do this if you store the engine for long periods of time. Especially the smaller models can suffer from this pollution because their power is relatively low .
In my experience lubricating with oil is fatal in almost all cases: the engine runs bad or even not at all with that. Mind that the flame gases at 1000 ° C hot and for that no oil is resistant. It creates a quick touch of burnt oil together with residues of flame gases. Lubricate with fine and dry graphite powder (scraped from a lead pencil) or a little WD40 can be done and in some cases and provides some relief.
The degree of contamination depends strongly on the materials used for the cylinder and the piston (see under point 3.)
2. Making the piston nicely fit in its cylinder.
The engine power is generated at the moment that the hot gases cool down in the closed cylinder so that there is created a partial vacuum in the cylinder. In order to exploit this under pressure maximum leaks must be minimized as much as possible. It is therefore important that the piston fits into its cylinder with a small clearance up to 0.03 mm maximum, and that the slide valve is nicely flat and fits nicely against the flame hole of the cylinder.
The bore in the cylinder must be well cylindrical and smooth. The best way to make a cylinder bore nicely and smooth cylindrical is honing. But not all modellers (like me) do not have the equipment for it. Therefore, I follow these steps:
Drilling the cylinder bore globally and than lathe it to the desired diameter with about 0.1 mm under size. Then ream the hole manually with an adjustable reamer because the reamer than will find its way itself in the cylinder bore. Clamp the reamer in the vice clamps with the flat end of the cone, so not turning the reamer but the cylinder manually over the reamer with ample oil. Turn the cylinder around and around with the same reamer adjustment until the cylinder is moving smoothly over the reamer. Then repeat this procedure with a fractional larger reamer adjustment. Repeat these operations until there is actually no diameter difference any more measurable over the entire length of the bore.
The diameter which is created now need not be exactly complementary to that of the drawing, because the piston will be made hereafter appropriate in the cylinder as follows:
Turn the piston until it fits somewhat "hooking" in the cylinder. Polish the piston manually in its cylinder with a fine abrasive paste (eg car cleaner Commandant nr. 4 as used for wearied auto car lacker) until a fits nicely with a clearance of 0.02 mm or less! The result is that the friction is so low that the motor rotates "as driven by the wind " while there is plenty of compression, even without piston rings that cannot be applied with these kind of small flame-eaters because they create far too much friction.
This way of making the cylinder bore is working very well and can compete with honing. At least it works well with pearlitic cast iron ( GG25 ), mainly because this material is "gritty" and therefore allows easy machining. This material is nevertheless very wear-resistant, is somewhat self lubricating due to the relatively high carbon content (about 8%) and does not have the tendency to dig into when the piston is running up and down in the cylinder.
If you don't have the availability over an adjustable reamer you also can turn out the cylinder bore smoothly with a sharp turning tool with a low feed rate and always from the outside in. After the last turn loose the turning tool from the cylinder you withdraw it. If the lathe is properly aligned the hole will also be nicely cylindrical (less than 0.02 mm taper). If that is not the case you need to clean up the hole with a sharp reamer with a low speed and ample oil. Then polish the piston in the cylinder as described above.
3. The material for the cylinder, the piston and the slide valve.
First of all, it is important that the thermal expansion of the piston material is equal to or smaller than that of the cylinder in order to prevent jamming of the piston when it is growing hot which it always the case with flame-eaters.
A good choice for the material is pearlitic cast iron ( GG25 ) for both the cylinder and the piston. This material is very durable, somewhat self lubricating due to the high carbon content and can be very easy machined due to the somewhat "gritty" behaviour. The disadvantage is that this material is quite corrosive and regular cleaning as described in item 1 will be more or less often necessary.
An alternative is stainless steel for the cylinder and a stainless steel or cast iron piston. A disadvantage of stainless steel is that machining is harder. Also here regular cleaning will be necessary from time to time.
Graphite is ideal as material for the piston because it does not corrode at all. In that case the cylinder can be also made of bronze or a good (hard ) type of aluminium alloy.
The slide valve also becomes very hot and should therefore be made of stainless steel. The interfaces of this valve and the surface surrounding the flame hole in the cylinder must be made perfectly flat and smooth with a sharp cutter. Except very light de-burring with polishing cloth don't grind these surfaces manually with sand-paper, because then quickly bulging of the surfaces can occur, hardly visible but possibly causing leaks along these planes.
4. The adjustment of the flame-eater.
The correct movement pattern of the slide valve in the 360° cycle is crucial.
The valve must open the flame hole in the cylinder about 30° before the piston is in its position closest to the cylinder head. The reason for that is that the cooled flame gases also are compressed again to atmospheric pressure during the working stroke of the piston already before the piston has reached its end position. If the flame hole is opened too late a counter-acting pressure will occur in the cylinder; the engine slows down or even stops running than. This opening of the cylinder hole through the slide should preferably be as abrupt as possible. During this 30º the cooled gasses with atmospheric pressure escape trough the flame hole to the outside. The valve must close the flame hole again at the time the piston is arrived again at 20 to 30 º from the other end side of the cylinder.
The overlap of the valve over the flame hole at the time that this is closed needs to be close to zero. I even have the experience that the motors run better if there is a very small gap left with the thickness of a human hair! For this phenomenon I still don't have a good explanation yet, presumably this also has to do with the occurrence of any counter-acting pressure in the cylinder.
The pressure of the spring(s) that holds the slide valve against the cylinder surface need to be adjusted so that the valve moves very well parallel along the cylinder surface but with a minimum pressure to minimize frictions. In fact, the valve only needs to be kept in place because the partial vacuum in the cylinder will pull the valve to the cylinder surface making a good leak free contact.
5. The spirits flame.
The size of the flame and its position in front of the flame hole in the cylinder is rather critical and very important for the engine's performance. It is recommended first experiment with this before making the final implementation of the spirits burner and its position relative to the flame hole. The bottom line is to avoid sucking-in false and cool outside air together with the flame gasses. It is my experience that the flame should be about twice as wide and high than the flame hole so that there is a large overlap. This is also the reason that flame-eaters are quite sensitive to drafts that the flame makes fluttering causing sucking-in some false outside air.
The use of ethyl alcohol (96 to 98 % ) has some advantages over household spirits, that also contains 2% methyl alcohol and 10 % water. The flame of ethyl alcohol is hotter, odourless and causes less pollution in the cylinder.
4. Flame-eaters with an internal valve
In particular in order to eliminate the rather critical adjustments with external valve flame-eaters I have designed and made flame-eaters with an internal valve which opens the flame hole on the inside of the cylinder instead of on the outside. In fact, this valve is a second piston that is made of the same material as the working piston.
For this construction and the important benefits of it see the page of the 1-cylinder version.
I also made 2-cylinder version and a version with a glass cylinder having a piston and a slide that has both are been made from graphite. This latest version has the important advantage that it does not pollute at all and therefore does not require any maintenance because graphite and glass does not corrode in these circumstances. A nice feature of this third version with glass cylinder is that the displacer is driven by a unique magnet system.